One of
the most important elements of the Flowdrill
process is the use of specified rotational speeds
or RPMs. The Flowdrill process requires higher
speeds than conventional drilling methods. Speed
requirements are influenced by the hole diameter,
material thickness, and the type of
material.
- Rotational speed requirements range from
1000 to 3500 RPMs.
- Motor power requirements range between
1.5 and 3.5 kWs.
|
|
|
 |
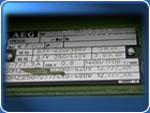 | |
|
|
Feed is
the rate that the Flowdrill advances into the
material. Manual, Steady or Variable feed rates
can be applied depending on the machine’s
capabilities. Flowdrill has tables to help you
determine the optimal feed values depending on
your material type and
thickness. | |
|
|
Axial
Force
Axial Force is the
downward pressure exerted on the material as the
Flowdrill advances into the workpiece. Thin
materials may bend or collapse under excessive
pressure. Adequate support must be provided to
prevent deformation. A pre-hole or a Fluted
Flowdrill may also be used to facilitate the
initial entry into the workpiece with reduced
axial force.
|
|
|
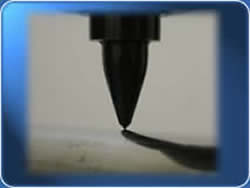 | |
|
|
|
|
Toolholders
The MC2
and MC3 Toolholders insure the optimum clamping of
the Flowdrills and prevent rotational slippage
while the tool is turning at high speeds. Multiple
prongs in the Collet securely hold the Flowdrill
in a 360° clamping system. The Toolholders use a
built-in aluminum cooling disc designed
specifically to diffuse heat that travels up the
spindle. The Toolholders use a standard tapered
shaft that will fit most standard drilling
systems. A cylindrical shaft is also available for
CNC machines.
|
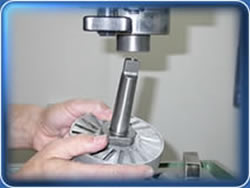 |
| |
|
|
Lubrication
To optimize the quality and precision of
the hole, lubrication needs to be applied prior to
each perforation. Lubrication can be done by hand
or with automatic spraying systems.
|
|
|
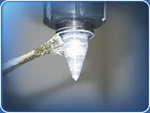 |
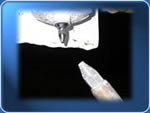 | |
|
|
|
|
Preholes
Preholes can be used to reduce the axial force
or to reduce the total length of the formed bush.
Using a prehole also produces a smooth finish in
the bushing’s lower edge. Reduced axial force may
be required to avoid bending thin materials (less
than1.5mm). |
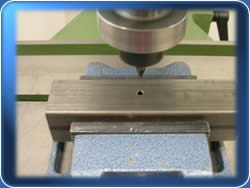 |
| |
|
Recommended Practices for Optimum
Results
- Use of equipment with the recommended
power and speed specifications
- Use of recommended Toolholders
- Regular inspection and adjustment of the
clamped Flowdrill tools
- Proper setting of the start (zero) and
final positions
- Use of recommended feed speeds according
to the type and thickness of material
- Proper lubrication of the Flowdrill
tool
- Secure and normal or perpendicular
clamping of the workpiece
|
|
|
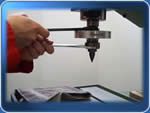 |
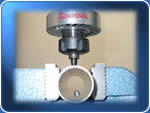
|
|
|
|